En el artículo en el que nos centramos en la Ley de Moore, quedó claro que toda la tecnología de semiconductores moderna está vinculada a dos factores: el tamaño de los elementos que se pueden integrar en un chip y su cantidad máxima. Para entender cómo funcionan las especificaciones de tecnología de "tantas micras" de hoy en día para indicar el trabajo del proceso de fabricación de chips, es interesante revisar brevemente cómo se fabrican los circuitos integrados, es decir, las tecnologías utilizadas en los circuitos integrados. Ese es precisamente el tema de nuestro artículo.
Retrocediendo un Poco en el Tiempo
Hasta 1950, cualquier equipo electrónico estaba compuesto por componentes individuales (discretos) que debían fabricarse por separado, cada uno con su propio proceso específico, y luego montados e interconectado en una placa común o chasis para formar el circuito deseado.
Todo esto cambió con la invención del circuito integrado por John Kilby en 1950, como narramos en el artículo anterior. La idea básica de Kilby era que en lugar de fabricar los componentes de un circuito por separado, y luego interconectarlos formando el circuito deseado, podríamos utilizar un solo proceso para fabricar todos los componentes interconectados en una plaquita de silicio, ya formando el circuito deseado.
La idea floreció, y los "circuitos integrados" comenzaron a aparecer.
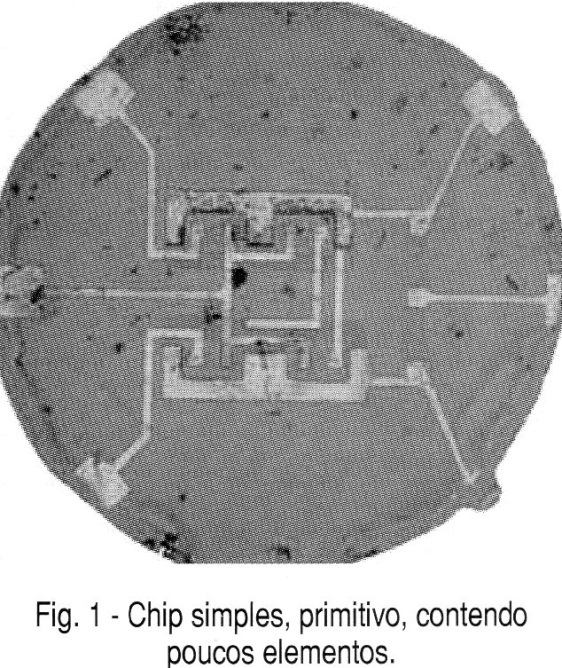
Partiendo de los tipos más simples, y la evolución de las tecnologías fue permitiendo la colocación de un número creciente de elementos en un inserto de silicio y también la reducción cada vez más marcada de las dimensiones de estos componentes.
La evolución de las tecnologías electrónicas se asoció precisamente con la evolución del circuito integrado en sí, como vimos cuando analizamos la Ley de Moore.
Por lo tanto, cuando hablamos de electrónica moderna y tenemos la intención de hacer de cualquier tipo de predicción el futuro, analizando qué tipos de nuevos dispositivos pueden aparecer, siempre debemos tener en cuenta las tecnologías de fabricación de circuitos integrados.
Precisamente los nuevos dispositivos que se pueden crear y la cantidad de componentes que se pueden integrar en un solo chip dependen de estas tecnologías.
Especificar el grado de elaboración de un CI es común utilizar dos parámetros importantes que son realmente interdependientes: la cantidad de componentes que se pueden integrar en las virutas y las dimensiones mínimas de los detalles que estos componentes pueden tener.
Para entender cómo funciona esto, vamos a hacer una breve revisión de los procesos de fabricación de los circuitos integrados.
Fabricando un Circuito Integrado
El proceso de fabricación de un circuito integrado implica básicamente 5 etapas
El punto de partida para la fabricación de circuitos integrados (así como otros dispositivos semiconductores como transistores y diodos) es el wafer. Es un disco de silicio cristalino extremadamente puro con un espesor de unos pocos milímetros.
El diámetro de los wafers varía según la tecnología utilizada y puede comenzar desde 100 mm (4 pulgadas) y hasta 300 mm (12 pulgadas).
En un cristal, como lo que como lo que forma los wafers, los átomos se organizan con una orientación bien definida. Esta orientación debe tenerse en cuenta en el proceso de fabricación.
Así, para los wafers de 100, 125 y 300 mm, se hace un corte que sirve para indicar cómo se orienta el cristal. En los wafers de 200 y 300 mm la marca consiste en un pequeño desgarro, como se muestra en la figura 2.
Básicamente hay tres tipos de wafers: tipo puro que se utiliza para la fabricación de Cls, Epitaxial (Epi) que es un wafer formado por un solo cristal con una película depositada en su superficie y Silicon on Insulator (SOI) que consiste en una película de silicio de cristal depositada en una película aislante en el wafer que sirve como base.
Al analizar las tecnologías utilizadas en la fabricación de circuitos integrados, las dimensiones de los elementos son extremadamente pequeñas. A menudo hablaremos de micras, nanómetros e incluso dimensiones más pequeñas. Será importante que el lector tenga una idea de estas dimensiones a través de la siguiente tabla:
Valor comparativo-mil milímetros resultan en un metroUn millón de micras es igual a un metro; mil micras equivale a un milímetromil millones de nanómetros equivalen a un metro; mil nanómetros es igual a un micrómetro
Unidad |
Símbolo |
Valor comparativo |
Metro |
m |
- |
Milímetro |
mm |
mil milímetros resultan en un metro |
Micrómetro o micra |
μm |
Un millón de micras es igual a un metro; mil micras equivale a un milímetro |
Nanómetro |
nm |
mil millones de nanómetros equivalen a un metro; mil nanómetros es igual a un micrómetro |
Una idea aproximada de las dimensiones de los objetos conocidos puede ayudar al lector a entender cómo pueden ser los pequeños componentes electrónicos modernos. En la tabla siguiente se muestran algunas dimensiones:
Objeto |
Tamaño aproximado |
Grano de arena |
100 a 1000 μm |
Diámetro de un cabello |
30 a 200 μm |
gérmenes |
1 a 30 μm |
Partícula de humo de cigarrillo |
10 nm a 1 μm |
Virus |
3 a 40 nm |
Átomos |
0,2 a 0,3 nm |
El menor proceso de fabricación utilizado actualmente para circuitos integrados puede grabar detalles de 130 nm (0,13 micras). Sin embargo, algunos procesos en estudios alcanzan 70 nm (0,07 micras). ¡Podemos decir que un detalle con este orden de tamaño es muy cercano al de un virus grande y es mucho más pequeño que una bacteria!
El siguiente paso es cambiar las propiedades de las regiones específicas de los wafers para que los componentes deseados y los senderos de conexión se formen entre ellas.
Este proceso implica el uso de la Fotolitografía.
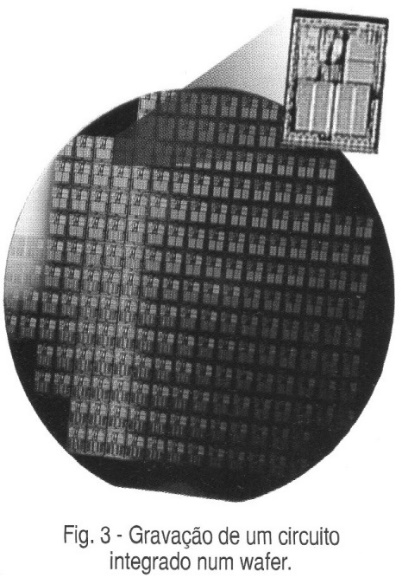
En la fotolitografía, un químico sensible a la luz llamado "foto resista" se extiende por la superficie del wafer, cubriéndola en la medida en que los componentes deben ser grabados.
El proceso de propagación de esta sustancia se realiza rápidamente y se controla con el fin de formar una película uniforme muy delgada. En la figura 4 muestra cómo se logra esto girando rápidamente el wafer.
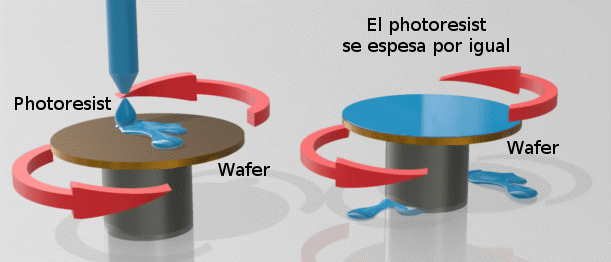
Después de eso, el wafer pasa por un proceso de cocimiento en un horno, después de lo cual se expone a la radiación ultravioleta a través de una máscara que tiene regiones opacas y transparentes, formando precisamente el diseño de los componentes que deben ser grabados.
El uso de la radiación ultravioleta es importante, como vimos en el artículo sobre la Ley de More, porque su longitud de onda más corta permite grabar detalles más pequeños.
Después de estar expuesta a la radiación, el wafer pasa por un proceso de revelación donde se retiran las áreas expuestas y las cubiertas permanecen. Varias variaciones de este proceso pueden ocurrir en este punto en la fabricación, pero lo importante es que, con la revelación, áreas conductoras y aisladas se registran en el patrón que corresponderá al circuito integrado, como se muestra en la figura 5.
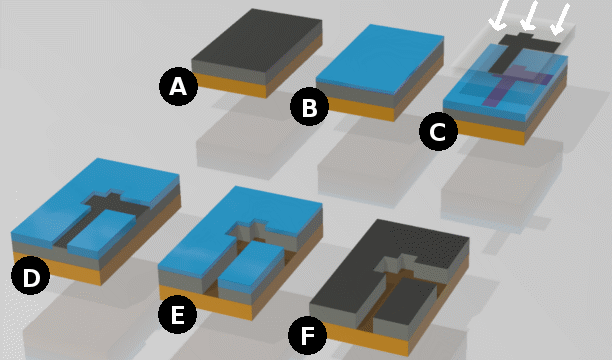
De una manera más detallada, podemos dividir el proceso de fotolitografía en seis fases:
Cubra el wafer con una sustancia que facilite la adhesión del photoresist
Cubra el wafer con un líquido fotosensible (photoresist).
Hornee el wafer para secar el photoresist
Exponga el wafer a la radiación ultravioleta a través de una máscara en la que esté presente el patrón a grabar.
Hornee de nuevo - algunos tipos de photoresist requieren que después de la exposición a la radiación haya un cocimiento para completar las reacciones químicas que ocurren.
Revele el photoresist eliminando la salida expuesta a las áreas que deben tener sus propiedades eléctricas alteradas, es decir, donde se deben formar los componentes.
Horneé el photoresist para estabilizar sus propiedades químicas
La siguiente fase en el proceso de fabricación es el despliegue de iones.
Lo que será cada región sensibilizada depende de las propiedades eléctricas que adquirirá. En el caso de los semiconductores, esto significa dopar esta región para que se convierta en un semiconductor N, P o incluso dejarlo libre de dopaje para que se convierta en una interconexión de componente o componente e incluso la armadura de un capacitor.
Esta implantación se realiza en una cámara de vacío. El wafer está conectado a un electrodo y los iones a implantar son acelerados por la tensión del wafer para penetrar la profundidad deseada, extendiéndose a través del material.
Un punto importante en el proceso de fabricación es precisamente la posibilidad de hacer que los iones penetren exactamente la profundidad deseada y el control exacto de la cantidad de los mismos. Las impurezas implantadas en este proceso no penetran más de unas pocas micras en profundidad en el wafer.
Continuando con el proceso de fabricación, además de la implantación de iones, varias sustancias se depositan en la superficie del wafer formando películas muy delgadas. Estas películas, como el nitrito de silicio, se utilizan para preservar la capa protegiéndola al final del proceso de fabricación. El poli silicio es otra sustancia utilizada para fabricar transistores de MOSFETs. Metales como el aluminio y el cobre también se pueden depositar para formar interconexiones entre los elementos del circuito.
Los medios químicos o físicos se utilizan para depositar el metal, dependiendo de la tecnología y el tipo de componente que se fabrica.
Finalmente, el wafer pasa por un baño químico. Se han desarrollado varias tecnologías que van desde el simple uso de líquidos hasta plasma, dependiendo del tipo de circuito integrado que se fabrica.
Una forma de baño se hace seca con el uso de ondas de radio, microondas de alta energía aplicados a un gas para que sea reactivo. Los gases que pueden ser ionizados resultando en cloro, bromo e iones de flúor se utilizan en algunos procesos.
Al final de todas estas etapas, en un solo wafer se pueden formar muchos circuitos integrados. La cantidad depende precisamente de las dimensiones de cada uno. En un wafer común se pueden fabricar más de 200 circuitos integrados a la vez.
Por supuesto, la presencia de impurezas en el propio material, fallas del proceso, hacen que no todos se utilicen. Así, antes de pasar el corte y encapsulación de cada uno de los circuitos integrados, se someten a una prueba de funcionamiento.
El resultado final es en la figura 6 en la que el pequeño chip de silicio resultante se suelda a los terminales de conexión y se encierra en un recinto que, si bien lo protege de la acción de los elementos externos, también sirve para disipar o transferir el calor generado en su proceso de funcionamiento.
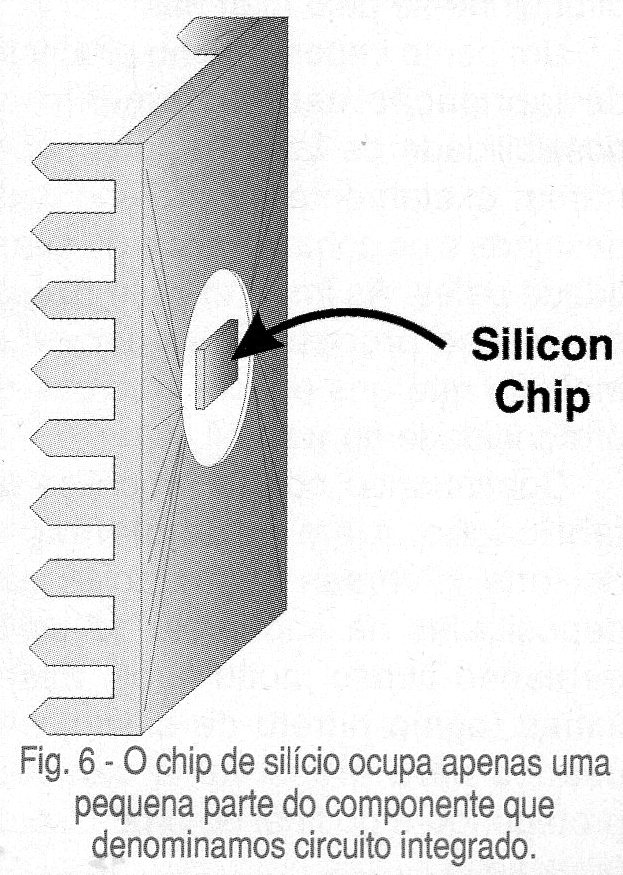
Conclusión
Las tecnologías de fabricación de los circuitos integrados han evolucionado para poder grabar detalles cada vez más pequeños en plaquitas de silicio y así aumentar la densidad de los componentes que se pueden integrar.
Esta capacidad se especifica en las tecnologías existentes y normalmente se expresa en forma de la medida del más mínimo detalle que se puede integrar con la definición.
Así, para DRAM y para microprocesadores que representan los componentes que cubren toda electrónica de circuito integrado, pasamos de una escala de integración de 100 micras en 1970 a menos de 0,18 micras en nuestros días.
En la figura 7 tenemos el gráfico que muestra esta evolución de las tecnologías de integración.
Como ya hemos señalado, los saltos tecnológicos pueden superar ciertos obstáculos determinados por las leyes de la física, como la relación entre la longitud de onda de la radiación utilizada en el proceso de litografía y el objeto más pequeño que se puede integrar.
El uso de radiación ultravioleta de longitudes de onda cada vez más cortas puede llevarnos a tecnologías mucho más pequeñas que las 0,07 micras pronosticadas para los próximos años, con una capacidad de integración de componentes que puede superar fácilmente la escala de terabits para las memorias.
Lo que tenemos que aprender es que incluso si las leyes de la física son válidas, nunca podemos dar definitivamente ninguna conclusión a la que hemos llegado, porque los saltos tecnológicos y los descubrimientos imprevistos pueden cambiarlo todo.